
I have a dream …
Bericht von Manfred
Leider ist der erste Teil des Bauberichtes nicht mehr auffindbar, so dass an dieser nur Teil 2 veröffentlicht wurde.
Diesen zweiten Teil meines Bauberichtes möchte ich mit dem Bau der Tragflächen fortsetzen.
Die Tragflächen werden mit Hilfe einer Helling erstellt, so spare ich mir den Aufwand jede Rippe mit Füßchen ausfräsen zu müssen.
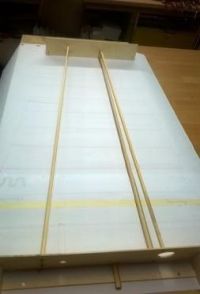
Der Plan der Tragflächen wurde im Vorfeld schon einmal ausgeplottet.
Die ersten Rippen und das Steckungsrohr werden der Reihe nach in die Holme eingesetzt.
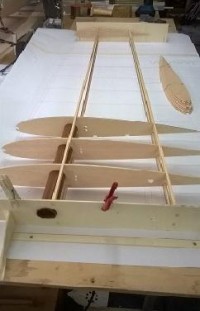
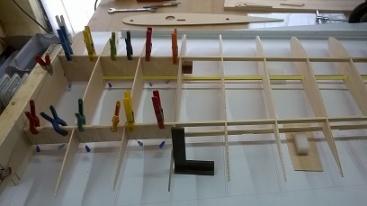
Die Holmverkastungen werden zugeschnitten. Die Rippen ausgerichtet und verleimt.
Hier entsteht das Querruder, in den Kiefernleisten sind bereits die Aussparungen für die Scharniere zu sehen.
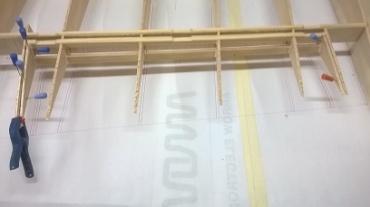
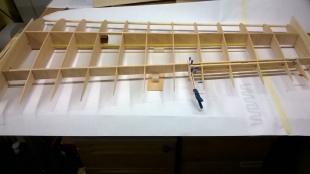
Alle Rippen und die Holmverkastungen wurden montiert bzw. verklebt.
Das Steckungsrohr ist eingebaut und verklebt. Durch das gelbe Röhrchen (Sangria-Trinkhalm) wird später das Servokabel gezogen.
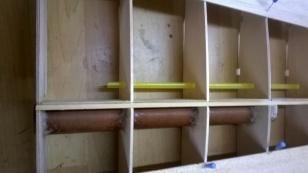
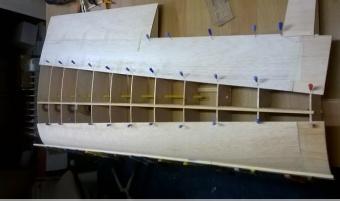
Ich beplanke mit einzelnen Brettchen und schneide diese dann passend zu, das spart Material.
Die vordere Beplankung muss natürlich gut gewässert werden, damit sie beim Biegen nicht einreist.
Nachdem die Tragfläche komplett beplankt ist, wird sie noch verschliffen, um anschließend mit GFK Gewebe versiegelt zu werden.
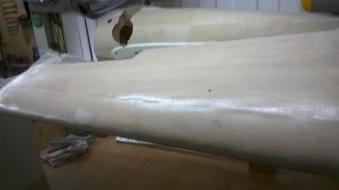
Für die Versiegelung verwende ich ein 20 Gramm Gewebe. Das Gewebe kann man nun mit verdünntem Epoxidharz, oder wie ich es gemacht habe, mit PU–Lack aufbringen.
Vorteil, PU-Lack ist fast geruchsneutral und das Werkzeug lässt sich einfach mit Wasser reinigen und die Trockungszeit ist nicht viel länger als bei Harz.
Die Entscheidung für PU-Lack liegt im wesentlichen darin begründet, dass man kein Lösungsmittel (Azeton oder Methanol) verarbeiten muss.
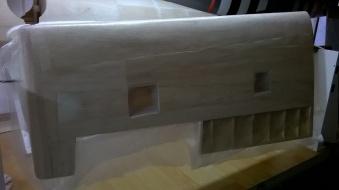
Das Aushärten der Tragfläche sollte in einer senkrechten Position erfolgen, damit sich die Tragfläche nicht verziehen kann.
Insgesamt habe ich 3 Anstriche mit PU-Lack durchgeführt, dies bedingt eine Gewichtszunahme von 35 Gramm.
Nach der Trocknung wird das überstehende Gewebe einfach mit dem Schleifklotz gekappt.
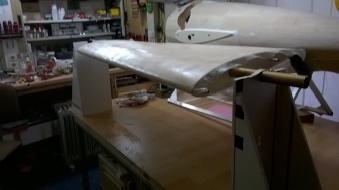
Als nächster Arbeitsschritt muss nun gespachtelt werden. Die Spachtelmasse wird aus PU-Lack und Talkum hergestellt und mit einem Japanspachtel aufgetragen.
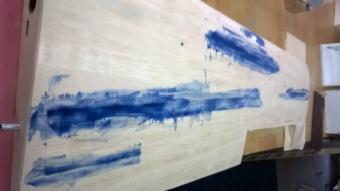
Die Spachtelmasse färbe ich ein, damit später zu sehen ist, wo schon gespachtelt wurde.
Und jetzt heißt es wieder schleifen, schleifen …
Anschließend wird das Ganze grundiert, um danach wieder gespachtelt und verschliffen zu werden.
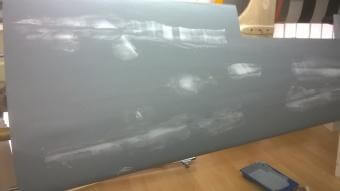
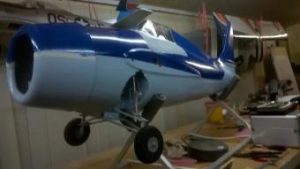
Wenn man mit dem Ergebnis zufrieden ist, erfolgt die endgültige Farbgebung.
Hier als Beispiel der fertig gestellte Rumpf.
Nach vielen Arbeitsstunden ist das Modell fertig aufgebaut und der Flugspaß kann beginnen. Ein kleines Video zeigt euch, Aufwand und Sorgfalt haben sich gelohnt.